If you’re an electrician or a seasoned electrical contractor, then it’s no mystery that understanding how to wire a safety switch is essential. They can make the difference between a minor scare and a life-threatening situation. Electrical faults can occur without warning. The risk of electrocution or fire significantly increases when installed incorrectly.
Wiring diagrams are essential tools for anyone working with electrical systems. They provide a visual representation of how electrical components are connected. The manufacturer usually provides these diagrams and includes detailed, model-specific wiring diagrams and instructions on how to connect each wire. This ensures you have the most accurate and up-to-date information for your install.
This article will discuss the general approach to understanding and using these diagrams for safety switch wiring installation. If you’ve been in the trade for a long time, this will serve as a simple refresher. Side note: feel free to check out the previous article, where we discussed the basics of safety switches and their critical contribution to modern electrical systems.
Need Safety Switches?
Get QuoteSell To Us
Got Electrical Equipment You Don't Need?

Reduce Your Electrical Inventories & Earn Cash
Sell My EquipmentPanelboard
Need a Panelboard for Your Project/Job?

Our Experienced Sales Engineers Can Help Design the Right Panelboard For You
Learn MoreTransformer Oil Testing
Is Your Transformer Due For Servicing?

Get Your Oil Analysis & Fluid Testing Done By Our NETA-Certified Techs
Learn MoreElectrical Product Resources
Product Training Product Safety Product Guides Product News Featured ProductsTools and Materials
Choose quality products that meet industry standards and are appropriate for the specific requirements of your installation. Check the list below before you dive into the wiring process.
Protective Gear | Safety glasses, insulated gloves, and a hard hat. |
Safety Switch and Enclosure | The safety switch for your application and any necessary enclosures. |
Mounting Hardware | Includes screws, anchors, or bolts suitable for installation environment (e.g., drywall, concrete, metal). |
Screwdrivers | A set of screwdrivers, including flat-head and Phillips sizes. Insulated screwdrivers are recommended to enhance safety when working with electrical components. |
Pliers | Needle-nose and side-cutting (diagonal) pliers will be useful for bending wires and cutting off excess material. Pliers with insulated handles offer an additional safety layer. |
Electrician’s Tape | Use high-quality electrician’s tape for insulating connections and marking wires, if necessary. |
Multimeter or Voltage Tester | Essential for verifying that power is off before starting work and for testing the installation once completed. A multimeter can also be used for troubleshooting electrical issues, such as continuity tests and measuring voltage, resistance, and current. |
Non-Contact Voltage Detector | A useful tool for quickly verifying the presence or absence of voltage without direct contact with the wire. |
Wire Strippers | Needed to strip insulation from electrical wires without damaging the conductor. Look for a model that accommodates the wire gauges you’ll be working with. |
Cable Cutters | For cutting wire to the required lengths. Make sure the cutters are capable of cleanly cutting through the wire sizes used in your installation. |
Conduit Bender (If Applicable) | For installations requiring conduit, a conduit bender is necessary to shape the conduit to the desired path. This provides neat and compliant installations. |
Fish Tape | For pulling wire through conduit or in walls, ceilings, and floors. This makes it easier to navigate wires through difficult or tight spaces. |
Grounding Equipment | Includes grounding rods and clamps if the installation requires additional grounding measures. |
Wire Nuts or Terminal Connectors (If Applicable) | For making secure wire connections, especially if the installation involves joining wires or extending circuits. |
Labeling Machine | For creating clear, durable labels for the safety switch and associated wiring. Proper labeling aids in future maintenance and troubleshooting. |
Step-by-Step Guide to Wiring a Safety Switch
Each safety switch will have specific wiring requirements based on its design and intended function. Find the wiring diagram for your particular safety switch product line or model. You’ll need to spend time understanding it by following the guide below. Here is an example of a wiring diagram from Schneider Electric Square D GEX75737 Safety Switch. If you need help finding the wiring diagram, contact the manufacturer’s customer support line, and they will direct you to the appropriate wiring diagram and resources.
1. Understand the Wiring Diagram
Identify Key Components
Identify all components depicted in the diagram, understand their physical configuration, and compare them with the actual components at hand. This includes power sources (e.g., mains supply), control devices (switches, relays), and output devices (lights, motors). Each component will usually have a symbol that conforms to industry standards, such as those outlined by the IEEE (Institute of Electrical and Electronics Engineers).
Decode Symbols and Notations
Familiarize yourself with the symbols and notations used in the diagram. This includes understanding the difference between solid lines (wires and connections), dashed lines (internal wiring of a component), and the various symbols for switches, resistors, capacitors, and more. The NEC (National Electrical Code) provides guidelines on standard symbols used in electrical diagrams.
Plan Wire Routes
Based on the wiring diagram, plan the route that wires will take from the power source to the safety switch and from the switch to the load. Consider the most efficient and safe routing. Verify that the installation will comply with all relevant electrical codes and standards. Diagrams may highlight important safety precautions or note specific considerations to keep in mind during installation.
Understand Control Logic
For complex installations, especially those involving motor controls or automation, you must understand the control logic from the diagram. Identify the logic behind the arrangement of control elements like switches, relays, timers, and sensors. This includes how safety switches are integrated into the circuit to interact with those other control elements and to respond to fault conditions.
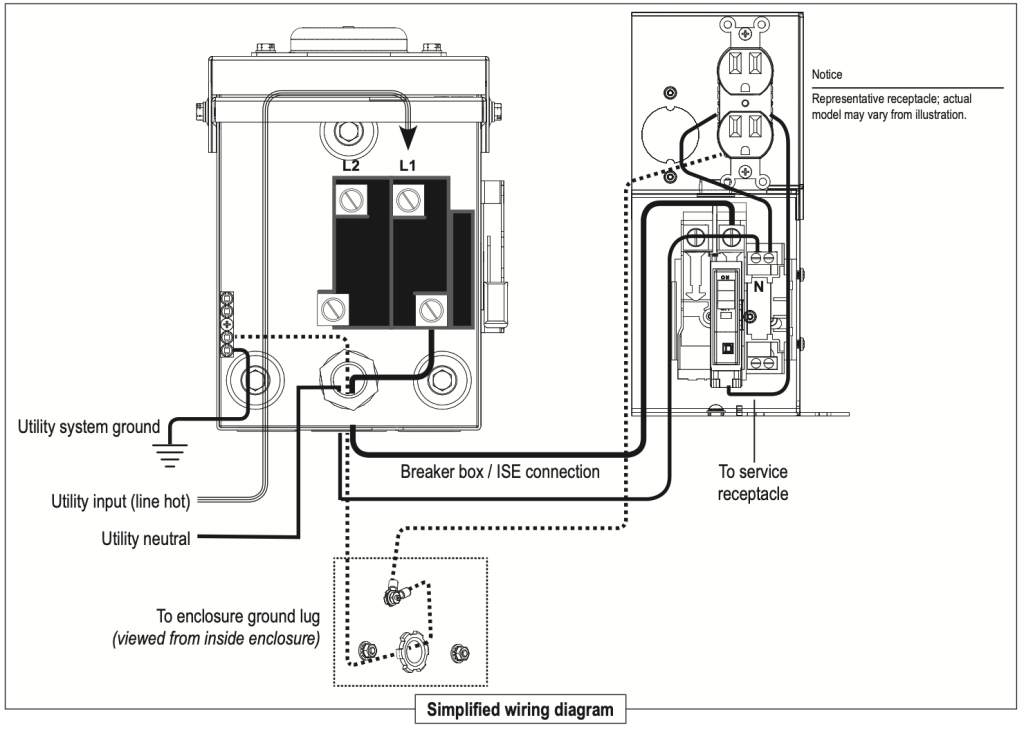

2. Prepare the Circuit
Safety First
Remember that you and any personnel involved must wear PPE (Personal Protective Equipment) to protect against electric shock and other hazards.
Locate the Main Circuit Breaker
Identify the main circuit breaker or distribution board that controls the power supply to the area where the safety switch will be installed. This is typically located in a central electrical panel for residential installations or a distribution room for larger commercial or industrial facilities.
Verify Circuit Identification
Before switching off the power, verify the correct circuit identification to ensure you’re disconnecting the power to the appropriate area. Misidentification can lead to unexpected live circuits, posing a safety risk.
Switch Off the Main Power
Turn off the main circuit breaker or the specific circuit breaker feeding the installation site. This action will cut the power supply, making it safe to begin work on the electrical system.
Lockout/Tagout (LOTO) Procedures
In commercial or industrial settings, follow lockout/tagout procedures to ensure that the disconnected circuit cannot be inadvertently re-energized while work is in progress. This involves placing a lock and a warning tag on the breaker to indicate that maintenance work is being performed.
Verify Power Is Off
Use a non-contact voltage tester or a multimeter to verify that power is indeed off in the area where you will be working. Test all wires that will be handled during the safety switch installation to ensure no voltage is present.
3. Prepare the Wires
Strip the Insulation
Use a wire stripper to carefully remove the insulation from the end of each wire that will be connected to the safety switch. The standard practice is to strip approximately 3/4 inch (about 19mm) of insulation. Do not nick or damage the wire’s conductive metal underneath, as this can create a weak point.
Inspect the Wire
After stripping, inspect the wire for any nicks or damage. Any compromised wire should be cut back to ensure only intact wire is used for connections.
Twist Stranded Wires
If working with stranded wire, twist the strands tightly together to form a uniform, solid end. This increases the contact area and improves the stability of the connection.
Tinning (Optional)
In some cases, especially when dealing with stranded wires that will be screwed into terminals, tinning the wire ends with solder can provide a more durable and reliable connection. However, this is not commonly required for safety switch installations and should only be done if specified by the manufacturer or in specific applications.
4. Connect the Safety Switch
Identify Terminals
First, identify the terminals on the safety switch where each wire will be connected. This typically includes terminals for the live (hot), neutral, and ground wires. The wiring diagram provided with the safety switch will indicate the correct terminals for each connection.
Secure the Live Wire
Connect the live wire to its designated terminal, often marked as “L” (L1, L2 for line connections) or colored differently. Insert the stripped end of the live wire into the terminal and tighten the screw securely without damaging it to hold the wire in place.
Connect the Neutral Wire
Attach the neutral wire to its corresponding terminal, usually marked as “N” or identified by a specific color. As with the live wire, make sure the connection is tight and secure.
Attach the Ground Wire
Finally, connect the ground wire to the ground terminal, often marked as “Gnd” or a green color. This connection is vital for safety, providing a path to ground (earth) in case of a fault.
Wiring Configuration
Look for any special instructions regarding the wiring of multi-pole switches or configurations that might be specific to certain types of equipment or applications.
5. Secure the Safety Switch
Mount the Switch
Position the safety switch in its designated spot, ensuring it’s accessible for operation and maintenance. Use mounting screws or bolts provided by the manufacturer or those that meet the requirements of the installation surface and environment. For outdoor installations, ensure the mounting hardware is suitable for exterior use to prevent corrosion.
Ensure Stability
Once mounted, check that all wires are neatly tucked away (no bare wires exposed). Make sure that the safety switch is securely fastened to prevent any movement that could loosen the connections over time.
Environmental Protection
If the safety switch is located outdoors or in an environment prone to moisture, dust, or chemicals, make sure it’s housed in a suitable enclosure that offers the necessary protection. Verify that the enclosure rating (such as IP65, IP67, etc.) matches the environmental conditions it will face.
6. Reconnect Power and Test
Re-energize the Circuit
After all connections have been made and verified, return to the main circuit breaker or distribution board to re-energize the circuit to test the install. If LOTO procedures were used, follow the proper steps to remove these safety measures and turn the power back on.
Verify Operation
With the power back on, test the operation of the safety switch. Activate the switch to ensure it correctly disconnects and reconnects power to the downstream circuit. Use a voltage tester or multimeter to confirm that power is appropriately cut off when the switch is in the “off” position.
Functional Testing
If the safety switch includes test functions or indicators, utilize these features to verify its proper operation. For ground fault circuit interrupters (GFCIs) or residual-current devices (RCDs), press the test button to ensure it trips the switch as expected.
7. Final Inspection
Inspect Connections
Double-check that wires are properly routed per the diagram. Make sure all electrical connections within the safety switch and at the terminal points are tight and secure. Loose connections can lead to arcing, overheating, and potential electrical fires.
Compliance Check
Review the installation to ensure it meets all relevant local codes and standards, like the National Electrical Code (NEC) in the United States or the Canadian Electrical Code (CEC) in Canada. This includes checking the wiring method, the type of safety switch used, and its placement in the electrical system.
Documentation and Labeling
It’s good practice to maintain detailed records of the installation process, including deviations from the original diagram. Clearly label the safety switch: include the date of installation, the type of safety switch installed, its purpose, its location, and any specific configurations or settings. This information is valuable for future maintenance or troubleshooting.
Client Briefing
If applicable, provide the client or end-user with a brief overview of the safety switch operation, including how to test it regularly and what to do if it trips. Providing this information helps ensure the electrical system is correctly used and maintained.
8. Troubleshoot Common Issues
If the safety switch does not function as expected, double-check the wiring against the manufacturer’s diagram. They can help you quickly identify where faults may occur. Check for common issues like loose connections or incorrect wiring. Make sure that the load is evenly balanced across phases and that the neutral is properly connected. An imbalance can cause unnecessary tripping. To identify leakage currents that may cause tripping, use a clamp meter around the ground wire. This can help pinpoint if leakage is occurring and its source.
Check for updates to safety switch technology and wiring standards. Manufacturers may release new guidelines that can aid in troubleshooting. Accurately diagnosing and resolving issues with safety switches demands a blend of technical skill, detailed inspection, and a methodical approach. Always prioritize safety and adhere to industry standards and regulations when performing any troubleshooting or repairs.
Maintenance and Safety Tips
Safety switch maintenance is important to ensure optimal performance and reliability. Not only does this safeguard the electrical systems you work on, but it also protects the lives of those who interact with them daily. As always, make sure the power supply is disconnected before performing maintenance or inspection work on safety switches. Remember to wear PPE.
Regular Testing and Inspection
Routine Checks: Implement a schedule for regular testing and inspection of safety switches in all installations. Monthly testing by users is recommended, but an annual inspection by a professional can catch issues that might otherwise be overlooked.
Test Functionality: Use the test button on each safety switch to verify operational integrity. Document and address any failures immediately.Visual Inspection: Look for signs of wear, damage, or tampering. Check that all connections are tight and that terminals have no visible corrosion.
Visual Inspection: Look for signs of wear, damage, or tampering. Check that all connections are tight and that terminals have no visible corrosion.
Calibration and Sensitivity Testing
Calibration Checks: Ensure the sensitivity of the safety switch meets the manufacturer’s specifications and regulatory standards. Use calibration equipment to verify that the switch trips at the correct fault current levels.
Environmental Factors: Consider the impact of environmental conditions such as temperature, humidity, and dust on the performance of safety switches. Adjust maintenance schedules and protection measures accordingly.
Documentation and Record Keeping
Keep detailed records of all maintenance, testing, and inspections carried out on safety switches. This documentation should include dates, findings, actions taken, and the personnel involved. In the event of a safety switch failure or incident, document all relevant information. This can provide valuable insights for preventing future issues.
Replacement and Upgrades
Be aware of the typical lifespan of safety switches and plan for their replacement before they fail. Manufacturer guidelines can provide insight into expected operational life. Stay updated on advancements in safety switch technology. Upgrading older systems can enhance safety and compliance.
Frequently Asked Questions
NOTE: This post is for educational purposes only. Electrical systems can be hazardous, and working with them without the necessary expertise and training can be dangerous. If you’re not a qualified electrician or don’t have experience wiring safety switches, it’s highly recommended to get the assistance of a certified electrical professional. Performing electrical work without the needed knowledge and training may lead to severe injuries, electric shocks, or damage to the equipment. Always prioritize safety and, when in doubt, contact a qualified electrician about how to wire safety switches and related electrical maintenance.